Understanding Wheat Drying: Essential Insights for Farmers
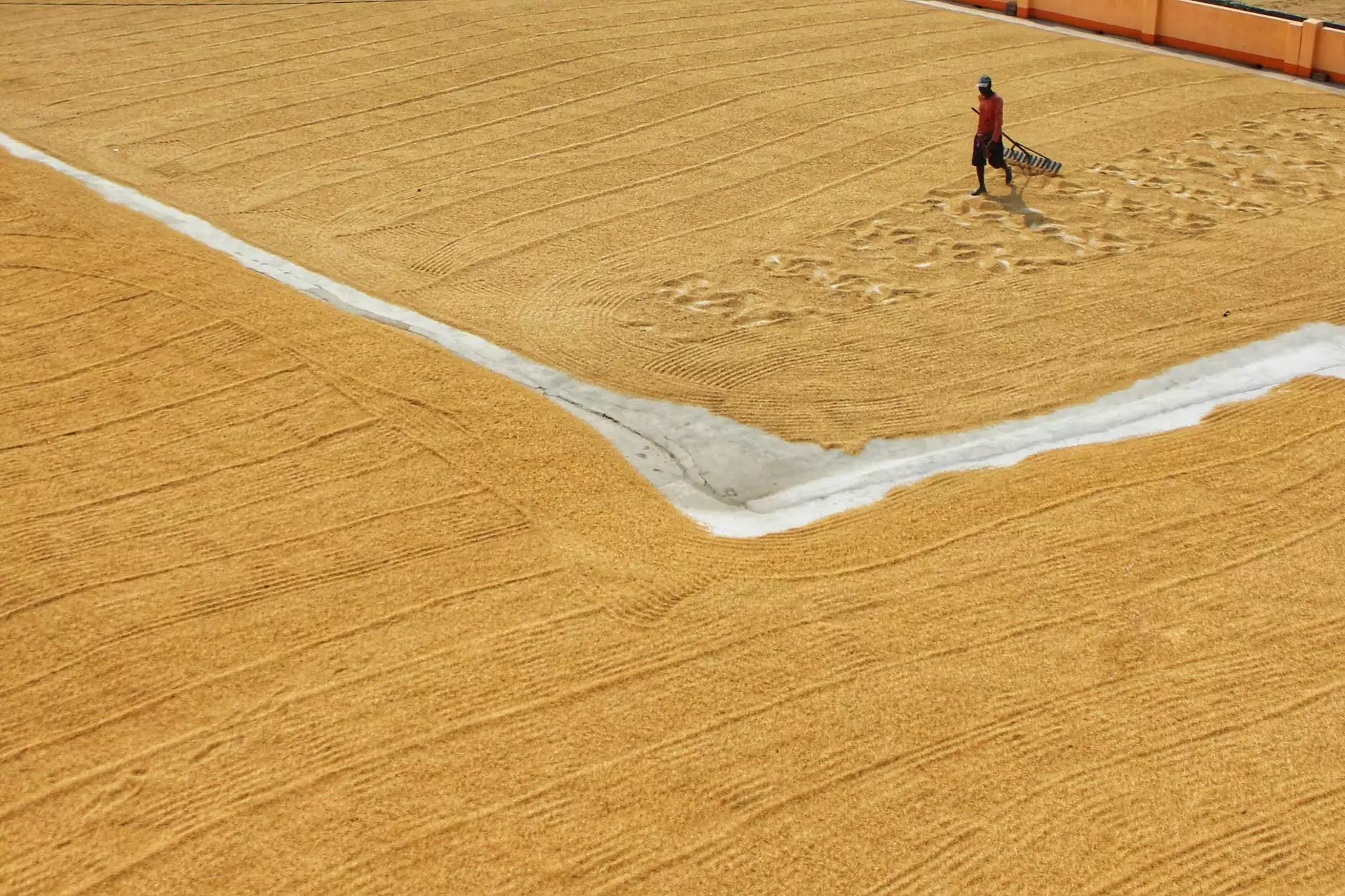
The process of growing wheat is intricate and demands careful management to ensure a successful harvest. One critical component of wheat farming is understanding what is dry for wheat, a concept that plays a vital role in determining the quality of the crop and its overall yield. In this article, we delve deep into the details of wheat drying, the methods to optimize this process, and the implications it holds for farmers.
Why Drying Wheat is Crucial
Wheat, like many other crops, requires specific conditions for optimal growth, including moisture content management during and after harvesting. The moisture level in harvested wheat can significantly affect its quality and storage potential. Here are key reasons why drying wheat is essential:
- Prevention of Spoilage: High moisture levels can lead to fungal growth and spoilage, making the grain unsuitable for sale or consumption.
- Improved Storage: Drier wheat can be stored for longer periods without risk of degradation.
- Market Standards: Many markets have strict moisture content requirements that must be met for successful sale and distribution.
What Constitutes 'Dry' for Wheat?
When we talk about what is dry for wheat, we are generally referring to the moisture content expressed as a percentage. For optimal storage and marketability, wheat should aim for a moisture level of around 12% to 14%. Let's take a closer look at what this means practically:
Understanding Moisture Content
Moisture content in grains is typically measured using several methods, including moisture meters and manual testing techniques. Here’s a breakdown:
- Moisture Meters: These electronic devices provide quick readings of grain moisture and are popular among farmers for their ease of use.
- Oven Testing: A traditional method where a sample of wheat is weighed, dried in an oven, and then weighed again to calculate moisture loss.
- Adherence to Standards: Each wheat type may have slightly different moisture content standards which should be researched prior to harvest.
The Impact of Environmental Conditions on Drying
The drying process of wheat can be heavily influenced by environmental conditions. Farmers must take into account the following factors:
1. Weather Conditions
Weather plays a pivotal role in the drying process. Hot, dry winds facilitate faster evaporation of moisture from the wheat grains. Conversely, humid conditions can inhibit drying, leading to increased moisture retention.
2. Harvest Timing
Harvesting wheat at the right time is critical. Waiting too long can expose the grain to rain or dew, while harvesting too early can result in high moisture levels. Recognizing the ideal harvest window ensures proper moisture levels from the outset.
3. Drying Techniques
After harvesting, there are several methods to dry wheat that are commonly employed:
- Natural Air Drying: This is the simplest method where harvested wheat is spread out in a ventilated area to allow air circulation to dry the grains naturally.
- Mechanical Drying: Using grain dryers offers a controlled environment for quick and effective moisture removal, enabling farmers to manage large quantities of grain.
- Combining Methods: Many farmers utilize a mix of natural and mechanical methods to optimize drying efficiency depending on their specific circumstances.
Measuring the Success of Wheat Drying
Measuring the effectiveness of the drying process is pivotal for guaranteeing that the wheat meets market standards. Regular monitoring of moisture content during and after drying is essential. Here’s how farmers can ensure their drying methods are successful:
- Regular Testing: Implementing a schedule to test moisture levels at different stages will help identify any issues early.
- Documentation: Keeping thorough records of moisture levels, drying times, and weather conditions can help refine future drying strategies.
- Adapting Techniques: Be prepared to adjust drying techniques based on the feedback from testing results and external conditions.
Common Challenges in Wheat Drying
The drying process is not without its challenges. Here are some common issues that farmers face:
1. Uneven Drying
Uneven drying can occur due to inconsistent distribution of airflow in dryers or stacking during natural drying. It is critical to ensure even spread of wheat to achieve consistent moisture levels.
2. Excessive Drying
While removing moisture is necessary, over-drying can lead to a decrease in grain quality, affecting seed viability and baking characteristics.
3. Equipment Malfunctions
Mechanical dryers can experience wear and tear. Regular maintenance is crucial to prevent downtime and ensure proper function throughout the drying season.
The Future of Wheat Drying Technology
As farming evolves, so too does the technology surrounding grain drying. Farmers are increasingly turning to advanced solutions to enhance the efficiency of drying. Here are some exciting developments in this area:
- Automation: Automated systems can monitor and adjust drying conditions in real-time, significantly improving efficiency and reducing labor costs.
- Smart Dryers: Incorporating IoT technology allows for remote monitoring and management of grain moisture levels, paving the way for data-driven decision-making.
- Renewable Energy Sources: Utilizing solar power for drying operations not only reduces costs but also promotes sustainability in wheat farming.
Conclusion: The Importance of Wheat Drying Knowledge
Understanding what is dry for wheat is an essential aspect of successful wheat farming. With the right knowledge about moisture levels, drying techniques, and environmental factors, farmers can ensure higher quality grain, better yield, and ultimately, greater profitability. By addressing the common challenges and adapting to new technologies, wheat producers will be better positioned to meet market demands and sustain their businesses in an ever-evolving agricultural landscape.
For more information on farm equipment repair and farming equipment needs, visit tsgcinc.com.