The Transformative Impact of Rapid Prototype in Metal Fabrication
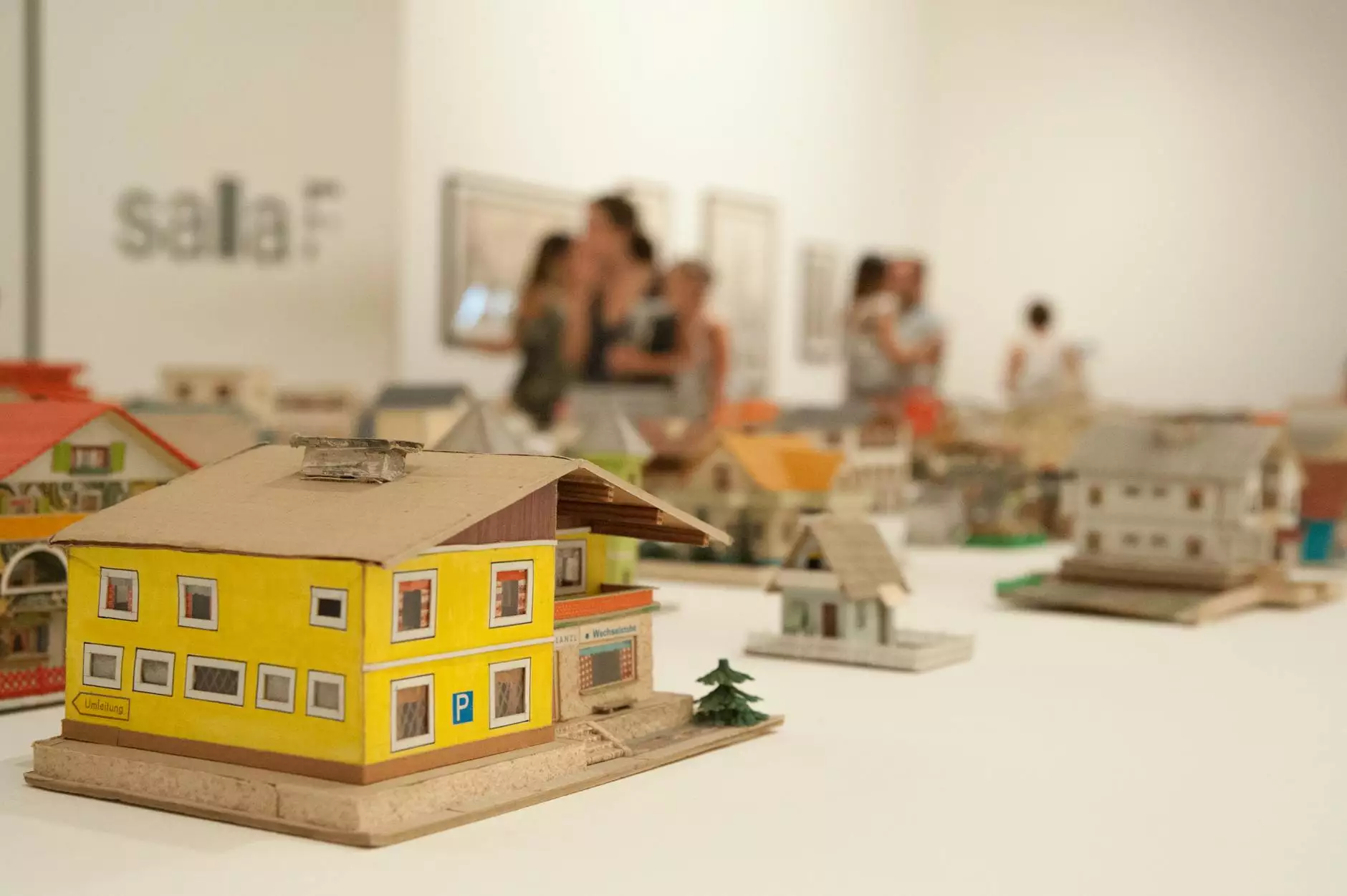
The world of manufacturing has witnessed a tremendous evolution over the past few decades, fundamentally changing how we approach design and production. Among the most significant advancements is the concept of rapid prototype technology. This innovative approach not only accelerates product development cycles but also enhances creativity and cost-effectiveness. In this article, we will delve into the various aspects of rapid prototype technology, its applications in metal fabrication, and how businesses like deepmould.net are leveraging these techniques to stay ahead in a competitive market.
Understanding Rapid Prototyping
Rapid prototyping refers to a series of techniques used to quickly create a scale model or functional prototype of a physical part or product. This process streamlines the design phase, allowing engineers and designers to test and iterate their concepts in real-time. Traditional methods of prototyping often involve lengthy timelines and considerable costs, making rapid prototyping a game-changer in industries such as metal fabrication, where precision and speed are paramount.
Key Components of Rapid Prototyping Technology
- 3D Printing: One of the most recognized forms of rapid prototyping, utilizing additive manufacturing techniques to build objects layer by layer.
- CNC Machining: Often used in conjunction with 3D printing, CNC machining provides high-accuracy prototypes from solid blocks of material.
- Injection Molding: Crucial for producing prototypes that require fine details and complex geometries, particularly in metal fabrication.
- Stereolithography (SLA): A 3D printing technology that uses light to cure liquid resin into hardened plastic, suitable for detailed models.
The Advantages of Rapid Prototyping in Metal Fabrication
Implementing rapid prototype methods within the realm of metal fabrication yields a multitude of benefits that can significantly enhance manufacturing workflows:
1. Accelerated Product Development
With rapid prototyping, businesses can dramatically reduce the time it takes to develop products. Traditional prototyping methods often require weeks or even months for completion. However, utilizing technologies like 3D printing or CNC machining can cut this timeframe down to days. This speed not only helps in meeting tight deadlines but also enhances the ability to bring products to market faster.
2. Enhanced Design Flexibility
The iterative nature of rapid prototype methodologies allows for continuous adjustments and improvements to designs. Engineers can make alterations in response to testing results quickly, leading to a more refined final product. This flexibility is essential for overcoming design challenges or integrating new features based on stakeholder feedback.
3. Cost Efficiency
By minimizing material waste and reducing labor costs associated with traditional fabrication processes, rapid prototyping represents a cost-effective solution for businesses. The ability to produce smaller batches and test designs without large upfront investment leads to significant savings throughout the product development lifecycle.
4. Improved Communication
Having a tangible prototype helps facilitate better communication between stakeholders, including designers, engineers, and clients. Visualizing a product through a prototype allows for clearer discussions on functionality and design elements, leading to more productive feedback sessions and collaborative decision-making processes.
Applications of Rapid Prototyping in Metal Fabrication
The versatility of rapid prototype technology opens up numerous applications across various sectors within the metal fabrication industry:
1. Aerospace and Defense
In the aerospace and defense sectors, where precision and performance are critical, rapid prototyping allows for the efficient development of components that meet stringent standards. Fast iteration cycles enable engineers to evaluate flight components for vibration, stress, and performance metrics accurately.
2. Automotive Industry
The automotive industry benefits immensely from rapid prototype techniques to produce car parts that are both innovative and compliant with safety regulations. By quickly testing and refining new designs, manufacturers can integrate cutting-edge technology into their vehicles to enhance performance and reduce costs.
3. Medical Devices
Metal fabrication for medical devices often requires bespoke solutions tailored to specific patient needs. Rapid prototyping enables healthcare companies to develop functional models that can be tested with patients, allowing for customization and quicker iterations while complying with regulatory standards.
4. Consumer Electronics
The consumer electronics industry is characterized by rapid innovation and frequent product launches. Rapid prototyping allows engineers to create prototypes for devices such as smartphones and laptops efficiently, facilitating prompt market introductions without sacrificing quality.
Future Trends in Rapid Prototyping
As technology continues to evolve, the future of rapid prototype in metal fabrication looks promising. We can expect to see advancements in:
1. Materials
New materials such as advanced alloys and composites will likely emerge, allowing for greater strength and lighter components in prototypes. Innovations in material science will facilitate the creation of prototypes that more accurately reflect the properties needed for final production.
2. Automation and AI Integration
The rise of automation and artificial intelligence can enhance the rapid prototype process, making it more efficient. AI can assist in analyzing designs, automating adjustments, and optimizing production parameters to improve outcomes further.
3. Sustainable Practices
As environmental concerns grow, sustainable practices in rapid prototyping will become increasingly critical. Innovations that minimize waste, utilize eco-friendly materials, and promote recycling in the prototyping process will gain traction.
Conclusion: Embrace the Future with Rapid Prototyping
In conclusion, the integration of rapid prototype technology in metal fabrication is revolutionizing the way products are designed and produced. The benefits of accelerated timelines, improved cost management, enhanced communication, and the ability to innovate are just a few reasons why businesses, particularly in sectors like aerospace, automotive, and medical devices, must embrace this evolution. Deepmould.net stands at the forefront of this movement, committed to delivering high-quality, precise fabrication solutions that meet the myriad needs of our clients.
As we look toward the future, organizations that leverage rapid prototyping will undoubtedly maintain a competitive edge, driving further advancements and setting new standards for excellence in metal fabrication. It is an exciting time filled with opportunities for growth, innovation, and success.